Concrete repair needs to be done properly and must be based on the cause of the damage. Major structural repairs should be supervised by a qualified professional engineer experienced in concrete construction.
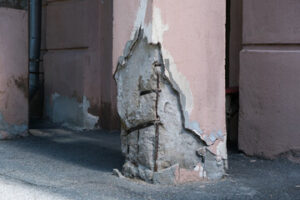
Knowing the right concrete repair products and techniques can help save you money and prevent future problems. These tips can help you tackle common concrete problems and get the job done quickly and efficiently. Visit Website to learn more.
Cracks are a common sign that it’s time for concrete repair. However, the type of crack and its location will determine whether you can repair it yourself or need to bring in a professional contractor.
Early-age cracking (sometimes called plastic shrinkage cracks) usually does not impair the general integrity of a concrete element and only impacts on its aesthetic appearance. It may, however, provide a passageway for moisture, dissolved salts and other deleterious substances that can lead to deterioration, corrosion of reinforcement steel and spalling if left untreated.
Most cracks can be repaired by applying a suitable concrete repair product to the damaged surface. Concrete patching products are available in latex, epoxy and polyurethane formulations to suit different types of damage and repair needs. It’s important to choose the correct product for the job and follow proper application techniques to ensure a long-lasting repair.
Cracks caused by soil movement need to be repaired with a special backfill material. It’s also important to correct the underlying issue that is causing the slab to shift in order to prevent the crack from reoccurring once the patch has been applied.
Concrete cracks that are heaving or pushing upwards or outwards need to be repaired by a professional contractor. These cracks often indicate a structural problem and can be caused by soil instability, improper site preparation or poor ground conditions.
When repairing heaving concrete, it’s important to use a highly durable patching material that is compatible with the surrounding concrete and will not contaminate adjacent surfaces. If the cracks are extensive, a full concrete replacement might be required.
It’s also a good idea to regularly inspect concrete for signs of aging and potential problems, especially after storms or other weather events that can cause surface movement. When possible, it’s a good idea to get estimates from multiple repair contractors before hiring one to work on your project. And, always take the time to thoroughly walk through a repair area with the contractor before handing over any cash so you both have an understanding of what will be done and what needs to be addressed.
Leaks
Most plumbing leaks, such as those from a dripping faucet or around a toilet base, are easy to spot and fix. But some leaks are more difficult to detect, such as a slab leak beneath the concrete foundation of a home. These hidden leaks can cause significant damage and increase water bills if left unchecked. Slab leaks are also a risk factor for structural damage to a building and must be addressed quickly.
Slab leaks develop when the plumbing lines beneath a house fail, usually due to poor installation or ground shifts. The shifting soil weakens and cracks the pipes that run through it, resulting in water leaks. These leaks are very difficult to identify and address, which is why it’s so important to know the signs of a slab leak.
These include damp spots on walls or floors, puddles of water, a sudden spike in your water bill, mold or mildew growth under floor coverings and unusual sounds like a gurgling or rushing sound when no taps are turned on. If you notice any of these symptoms, call a plumber to investigate.
A professional plumber can use a variety of techniques to locate and repair a slab leak. The most traditional approach involves precisely locating the leaking section of pipe using specialised equipment and breaking through the concrete to access it. The plumber can then cut out the faulty section and replace it with new copper or chlorinated polyvinyl chloride (CPVC) pipes.
Other ways to repair a slab leak include trenchless methods, such as pipe lining and resin injection. These methods involve less disruption to your property and are usually cheaper than traditional pipe replacement. However, they are not appropriate for all leaks and can be limited by the accessibility of the leaking pipes. If you have a very extensive pipe network with numerous leaks, a full re-piping may be necessary. This can be expensive, but it’s the most effective long-term solution for your home. Contact a professional plumber to find out more about the different options available for your home and to discuss your budget.
Loose Joints
Concrete is durable but it can be damaged by traffic and weather. Whether your concrete is in a warehouse with heavy forklift traffic or outside where the sun beats down on it all day, a lot of wear and tear can damage concrete joints. Loose joints can lead to cracking, heaving, and structural damage. A little preventative maintenance can help you avoid costly repairs down the road.
Control joints are a good idea in slabs but they need to be stabilized with an effective joint sealant. When a concrete control joint is too loose, it can lead to slab movement which can cause cracking. Loose joints can also create passageways for water and ice. Depending on the location of the joint it may be necessary to repair the slab to prevent further damage.
Loose expansion joints can be a problem in concrete pavements as well as industrial floors. Unlike asphalt expansion joints, which tend to self-seal and hold up against petroleum spills, concrete expansion joints can get loose because of dry shrinkage. The best way to prevent loose concrete expansion joints is to use a quality concrete patching and sealing product such as QUIKRETE Non-Sag Polyurethane. It is easy to apply, can be used in wet conditions and dries quickly.
Other types of concrete joint repair products include Trim-A-Slab, a rubber-like material that flexes and holds itself in the gaps between slabs. It is resistant to rot, moves with the slabs during expansion and contraction, and doesn’t trap dirt or debris like wood.
Another good choice for a concrete joint repair product is POLYFLEX moisture insensitive epoxy. It is self-leveling and can be applied to masonry joints, saw cut control joints and cracks. POLYFLEX adheres strongly to concrete and can withstand the stress of vehicle vibrations.
Once the joint is sealed, you should tap it gently with a hammer or other dull object to check that the bond has held. If you hear a hollow echo then the bond hasn’t worked and the joint will crack in time. You can also test a concrete joint by tapping it with your finger. If it sounds a dull thud, then it has bonded.
Structural Damage
Structural damage to concrete structures may occur from a variety of factors. It can be the result of expansion and contraction of the structure caused by temperature changes, seismic activity or rebar corrosion. In these cases, a structural repair method is required. Structural repairs should only be performed by qualified professionals as the repairs can have a profound impact on the safety and stability of the structure.
Many structural repair methods are used to restore damaged and deteriorated concrete structures. A common technique is concrete injection, which involves injecting a liquid material into the damaged structure to fill cracks, strengthen and stabilize the surface and fill voids. Another popular method is concrete leveling, which uses polyurethane to raise sunken and cracked concrete surfaces back to their original, even state. Concrete leveling can be done on sidewalks, driveways, patios, garages and pool decks.
When it comes to repairing structural concrete damage, the quality of the materials used is critical. There are a number of properties that are important to the durability of repair materials, such as cracking resistance, permeability and freeze-thaw durability. Other important characteristics include abrasion resistance, chemical resistance and tensile strength.
The type of concrete repair required will depend on the cause and extent of the damage. Using surface repair methods on structural damage can lead to poor adhesion and a temporary solution. Structural repair methods require extensive preparation and curing processes to ensure the longevity of the repair.
Often, small cracks and spalling can be repaired by simply patching the area with a commercial concrete repair product. It is important to regularly inspect the concrete for signs of deterioration, as ignoring them can lead to more serious problems in the future.
Regular maintenance and repair of concrete structures can increase safety, extend their lifespan and improve their appearance. It is also cost-effective to perform small repairs as they occur, rather than waiting until the concrete begins to break down and requiring costly replacements. In addition, addressing concrete issues early can prevent tripping and falling hazards, which can lead to accidents and injuries.