Before the roof itself is installed, your contractor will inspect and repair any underlying issues. This is especially important around chimneys, windows, and joints.
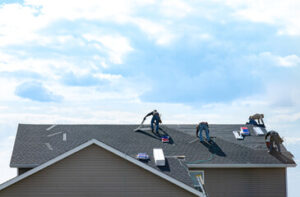
They’ll also install a drip edge and underlayment, and then add starter shingles. These first shingles are half as wide as regular shingles and create another watertight layer.
A roofing installation requires more preparation than you might expect. The roofers will need to cover landscaping, park a dumpster in the driveway, and lay tarps over any movable sculptures or plants. These precautions will help protect the exterior of your home from dust and debris during the roof’s tear-off and installation processes.
The first step in a roofing project is the removal of the old shingles and underlayment. This process may take a few hours, depending on the size of your roof and its complexity. While this step is essential, it also creates a mess. Roofing contractors must dispose of the old materials and any loose shingle fragments, which can cause damage to the yard and surrounding structures.
Once the tear off is completed, the contractors will begin installing new underlayment and flashing. These components provide a foundation for the new shingles and prevent moisture from entering the home. The contractor will also install a new layer of insulation, which will further improve your energy efficiency and reduce the amount of heat that is lost through the roof.
After the underlayment is installed, the roofer will shingle the top portion of the roof. This can be done in several layers or one complete row at a time. The shingles will be installed close together at the edges and spaced further apart in the center to ensure that water is not trapped behind the shingle and cause leaks.
When the roof is nailed, it is important that the nail heads are not left exposed and can’t be pushed in further by wind or rain. This is why it is a good idea to have a contractor who uses metal nails, which are more durable and resist corrosion over time.
It’s important to note that the pounding of hammers and impact of nail guns can cause vibrations inside your home, which can damage wall-hung paintings and other delicate items. For this reason, it is a good idea to remove these items before the work begins and place them in storage areas where they will not be disturbed.
Materials
A roofing project can’t go forward without the right materials. The list of supplies includes protective wear, tools for cutting and hammering and underlayment and shingles. The roofing material you choose can elevate your home’s appearance and add value to it. It’s important to consider the climate in your region and the manufacturer warranty when choosing a roof.
Asphalt shingles are the most popular roofing material in the United States because they’re affordable and easy to install. These shingles are available in different colors and styles to complement the architecture of your home. They’re also fire-resistant, and can withstand strong winds and heavy rains.
Clay or concrete tiles are another option for your roof. They give your home a Mediterranean look and are eco-friendly. They’re durable and last 40 to 50 years. They’re also non-combustible and require additional framing during installation.
Slate tiles are a beautiful and classic roofing material that enhances the beauty of your home. Slate is a natural stone product that’s long-lasting and resistant to fire, water and ice. It’s an expensive choice, but it can increase your home’s resale value and boost its energy efficiency.
Other types of roofing include metal, single-membrane systems like EPDM or rubber, thermo-polyolefin (TPO), and PVC roofing. These roofs are suitable for low-slope and flat roofs. They’re durable and rust-resistant and offer good protection against ponding water, hail, snow, and UV rays.
When installing a new roof, you’ll also need a gutter system and fascia boards. These pieces are placed along the eaves and valleys of your roof to prevent water from seeping into the rafters or trusses. They’re also essential for preventing leaks caused by ice dams and wind-driven rain.
A roof ventilation system is a must-have for any home, and it can be installed in addition to any type of roofing. This ventilation system promotes the natural flow of air through your attic to reduce overheating and moisture build-up, which can damage your roof.
Other roofing products include a mineral-surfaced leak barrier, which is critical to install at the eaves, valleys and around penetrations. It protects your roof from leaks and ice damming, and can help keep your home cool and comfortable all year round.
Installation
The installation process involves multiple tasks that need to take place. The first is the tear off of the old roof materials. Your contractor will cover sensitive areas of your home and yard with tarps and use wooden boards to protect the garden, air conditioning unit and other items from damage during the removal. They’ll also have a dumpster delivered to hold the old roofing materials and will put up protective barriers like fencing to keep the area safe for everyone involved.
Next comes the actual installation of the new roof. The roofers will lay the underlayment, which is a layer of material that’s installed over the shingles and helps to prevent leaks in the event of storm damage or other problems. Then they’ll install the shingles, starting at the bottom edge of the roof and working their way up. They’ll carefully overlap each shingle with the one above it and nail it into place using a pattern that includes close nails along the edges and more spread out ones in the middle.
They’ll also install any necessary vents for attic ventilation and may add a ridge vent to help with moisture control. Any flashing that’s needed for leak-prone areas will be installed too, including around chimneys, wood stove pipes and certain vents. The eaves will be protected with drip edge flashing and roof valleys with valley flashing. And any vents or other penetrations will be sealed with roofing cement.
Final Inspection
The final inspection, or closeout inspection, is often referred to as the “big day.” Just like a final exam, preparing for it begins long before that critical date. If you’ve done a thorough pre-purchase inspection, followed the recommendations in this series and built a good relationship with your inspector, the day should pass smoothly.
The last inspection is the opportunity for the inspector to walk the building and verify that the work completed meets the requirements of the permit. A number of issues are usually raised during a final inspection, which is why it’s so important to be conscientious throughout the process.
These issues may be minor and easy to fix—such as a broken window that requires closing the work permit or a wire that is exposed but covered by an outlet box—or major and urgent, such as a staircase that doesn’t meet egress requirements. These issues can be difficult to resolve on a timetable that is compatible with the schedule for finishing the project, and are a significant risk to passing the final inspection.
Many local building authorities and inspectors will provide a list of focus areas prior to the final inspection. This provides a chance for the contractor to understand what is expected and address any concerns ahead of time. Detailed checklists can also be found on the websites of some local municipalities.
During the penultimate inspection, it’s a good idea to ask your inspector what they will be looking for on the day of the final inspection and what documentation is required. That way, there won’t be any surprises that will slow the progress of the project or cause costly delays.
Whether the final inspection runs smoothly or is fraught with awful surprises is greatly dependent on the effective communication between the inspector and the construction team. This is why it’s so important to build a rapport with your inspector during the penultimate inspection. Ideally, the final inspection should be the culmination of an entire process that begins with designers submitting building plans and ending with the builder or general contractor obtaining a certificate of occupancy (CO). This means that everyone on the project has worked together in a positive manner, and all work is up to code and quality standards.