Unlike traditional manufacturing techniques, 3D printing is an additive process that builds up parts in layers. It starts with a virtual design made with CAD software.
That model is then sliced into hundreds or even thousands of thin, horizontal layers with slicing software before being sent to a 3D printer machine. Click Phoenix 3D Printing to learn more.
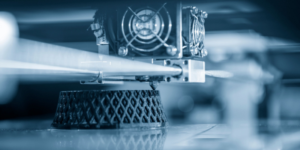
- Personalized Content
The 3D printing industry is fueled by various players, including printer manufacturers, material suppliers, and software companies. These players are the foundation of the market and dictate its direction.
3D printing involves creating three-dimensional objects through a layering process. It can create various objects ranging in shape, size, and rigidity. It is part of a larger family of manufacturing processes, sometimes called additive manufacturing.
This process offers many benefits, but the most significant is its ability to customize products. It is much faster than traditional manufacturing methods, like injection molding, and allows for rapid product design iteration. It also offers a lot of flexibility in terms of what materials can be printed. This is important because consumers have a lot of choices when it comes to personalization.
In addition, 3D printing is a great way to create customized medical devices and medication. It can be used to print custom-made medical models that help doctors plan their surgeries and print prosthetics for people who have lost limbs. It can also be used to create individualized medicine, a growing pharmaceutical industry trend.
Another area where 3D printing is making a big impact is food. Many people are concerned about the nutritional value of our diets, and 3D printing can offer a solution. For example, a company called Krill Design uses orange peels, lemon peels and coffee grounds to create furniture. The company even has a line of edible printer ink. While it might seem like something out of the Jetsons, continued research in this area could eventually lead to a future where people can print their own meals using nutritious ingredients.
- Speed
Whether you’re an amateur do-it-yourselfer tired of waiting for grass to grow or an industry titan looking for new ways to cut costs and production times, 3D printing offers a powerful way to get the job done. Advances in printer materials and core technologies have grabbed the most attention, but optimizing nitty-gritty motions and processes also yield huge gains in print speed.
One major factor in how long it takes to create a physical model from a digital design is the thickness of each layer of material that’s laid down. Thicker layers reduce printing time but may result in a loss of detail and rough surfaces. Thinner layers, on the other hand, improve resolution and smoothness but require more time to print.
Another big consideration is what type of material is used. While plastics like polylactic acid (PLA) are commonly used, there are other materials available that offer different advantages, such as metals or concrete. Some have even higher melting points, which allow them to be printed at a much faster rate than PLA.
Finally, the software program that prepares the 3D file for the printer — known as a slicing program — has a huge impact on print time. Advanced slicing programs can analyze models and adjust the settings for optimal efficiency. This includes making smarter decisions about the positioning and orientation of the model on the build platform, reducing or eliminating the need for support and saving time.
As technology advances, so too does the need for blisteringly fast 3D printing speeds. But pushing those limits risks quality—loss of detail, rough surfaces, or even print failures —and is often a trade-off that most users aren’t willing to make. With a few key tips, however, it’s possible to achieve faster print times without sacrificing quality.
- Customization
For too long, traditional manufacturing methods have prioritized efficiency and uniformity over personalization. But 3D printing offers manufacturers an opportunity to break free of those constraints and achieve mass personalization at scale. By enabling design freedom, precision customization, and consumer empowerment, 3D printing opens up endless possibilities for innovation and differentiation in a competitive marketplace.
The process begins with a computer-aided design (CAD) file, which can be created in software such as SolidWorks, Autodesk Fusion, Onshape, ANSYS, and others. The file is then exported as an STL, the universal input format for 3D printers. The printer then produces the part, layer by layer, in a material such as polymer, metal, or ceramics. In addition to producing parts with complex geometries that are impossible or impractical to produce through traditional methods, on-demand printing saves on tooling costs and accelerates time-to-market.
This ability to rapidly produce a prototype or a small production run of a product allows engineers and designers to develop their ideas more quickly and effectively, and get them to market faster. For example, engineers at Airbus used 3D printing to create 500 high-precision drilling caps for testing aircraft components, cutting the development time from weeks to three days.
In the medical field, Glazebrook predicts that 3D printing will further streamline the process of designing and manufacturing customized prosthetics and orthotics. And with more and more of these designs becoming digital, he sees a future where manufacturers will offer even greater personalization to patients.
The democratization of 3D printing has given rise to a new era of direct-to-customer business models, where manufacturers can use this technology to build a stronger connection with their consumers and increase revenue by offering personalized products at scale. Hasbro, for example, used 3D printing to create a personalized action figure for each of its customers during the COVID-19 pandemic, and Gillette is using it to give its customers the power to customize and manufacture their own razor handles.
- Reduced Costs
3D printing allows for an on-demand production model, which cuts down on storage costs and reduces inventory costs. With traditional manufacturing methods, companies often have to produce large inventories of products to cover unforeseen demand and ebbs in sales, and this can add up to significant overhead. In addition to reducing warehouse space and cost, on-demand production also eliminates the need for costly storage of spare parts.
This on-demand production model also reduces logistics and supply chain costs, because it eliminates the need to ship parts from far away. Local 3D printers are able to print high-quality, customized parts quickly and efficiently, and this means that businesses can cut down on the number of warehouses they need to maintain and significantly reduce their storage costs.
Another way that 3D printing can cut costs is by reducing material consumption. Traditional manufacturing processes typically use a lot of materials, especially when it comes to metals and composites. However, with 3D printing technology, companies can design structures and build models with the smallest amount of material possible, which will save on the overall cost of production.
Additionally, 3D printing can help to reduce building and construction costs by enabling the fabrication of advanced prototypes that are nearly identical to final products. This allows designers to test their ideas without having to invest in a full-scale product, which is often expensive and time-consuming.
Finally, 3D printing can eliminate redesign cycles during the transition to a high-volume production phase, which speeds up the time to market for new products and reduces financial risk. The 3D printing process is very accurate, and it can be used to create complex geometries that would not be possible or feasible with conventional construction methods. In addition, the ability to use multiple polymer materials, which vary in price and strength, allows for a variety of design iterations, reducing development time and speeding up product launch times.
- Sustainability
3D printing allows for the consolidation of several parts that would have otherwise been made separately into one, which can significantly cut manufacturing costs and time. This also reduces waste, as fewer materials are used per part and less glue is required. Additionally, the printing process can make the parts lighter than traditional manufacturing, which cuts energy use and emissions by reducing overall machine weight, Miller said.
The printing process can also create parts that are stronger than traditionally made ones, allowing them to last longer and potentially cut replacement costs. This may help businesses cut down on their supply chain costs and reduce the number of parts they need to stock, which can save money in shipping logistics and storage expenses.
As the industry grows, companies are looking for sustainable ways to print. For example, Jabil, one of the world’s largest contract manufacturers, is using 3D printing to produce parts that can be customized for specific applications. Its goal is to make the manufacturing process as green as possible.
Other sustainability benefits include the fact that printing a single unit eliminates the need for packaging, and printed parts can be lighter than those made with traditional methods. This can help reduce shipping and transportation costs, which in turn can cut down on fuel usage. Additionally, printed parts can be made in remote locations where supplies are hard to come by.
Many of the printing materials available are non-biodegradable, such as ABS or PLA filaments that use petroleum-based plastic. However, a growing number of filament makers offer plant-based or other sustainable alternatives. In addition, some companies have started to use recycled materials in their printing processes.